In the plastics manufacturing industry, balancing cost efficiency with sustainable practices has become increasingly important. As companies face growing environmental regulations, many must decide whether to manage plastic scrap recycling in-house or outsource it to a specialized provider. Both strategies have unique advantages and limitations, and choosing the right one depends on a business’s operational goals, available resources, and capacity for handling recycling operations.
In-House Recycling: Pros and Cons
- Control Over Quality and Consistency
In-house recycling provides complete oversight, ensuring that recycled materials meet internal quality standards. For manufacturers working with high-spec compounds, having direct control over recycling operations can ensure consistent material quality. This is especially important for applications requiring precision in material composition. - Efficient Production Flow
Recycling in-house minimizes turnaround times, as materials can be processed and returned directly to production without delays associated with shipping to third-party recyclers. This internal cycle also offers protection against potential supply chain disruptions, creating a more reliable flow of materials for production. - Enhanced Environmental Compliance and Brand Image
By managing recycling operations, companies can directly ensure environmental compliance, aligning with corporate sustainability goals and enhancing brand image. Handling recycling internally demonstrates a firm commitment to green practices and creates valuable opportunities for brand-name storytelling.
- High Costs and Capital Investments
In-house recycling requires significant initial investments in machinery, storage space, and skilled labor. Complex equipment, especially for managing mixed post-industrial materials, can carry high upfront and ongoing costs, including maintenance and training expenses. - Added Complexity and Resource Diversion
Running recycling operations within a manufacturing facility adds layers of operational complexity and administrative oversight. Training employees, performing maintenance, and handling compliance reporting require resources that might otherwise focus on core production activities. - Scalability Challenges
As production grows, scaling in-house recycling to meet increased demands may require additional equipment and space. This can be a significant limitation for companies with infrastructure constraints, potentially stalling their ability to manage larger volumes effectively.
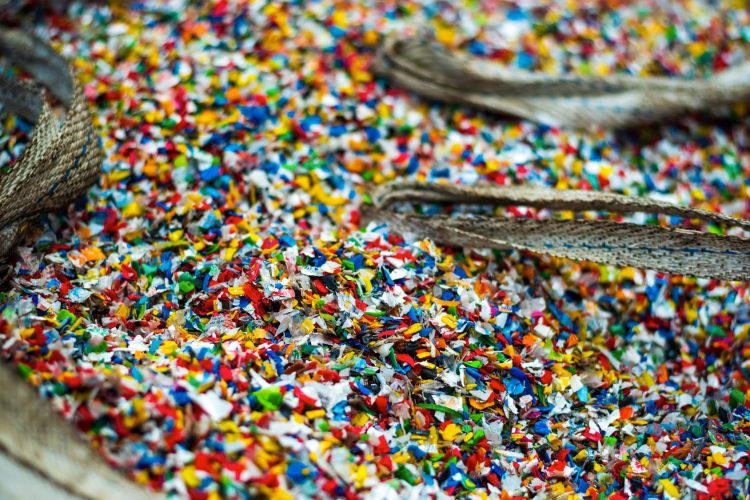
Image by frimufilms on Freepik
Outsourced Recycling: Pros and Cons
- Cost Efficiency and Access to Expertise
Outsourcing to a specialized recycler allows companies to avoid the high costs of setting up and maintaining recycling operations internally. By partnering with an expert like C-Square Polymer—recognized for its expertise in recycling diverse post-industrial materials—manufacturers gain access to industry-leading technology and processes without the capital burden. Our specialized knowledge in handling mixed materials means manufacturers can recycle a wider range of scraps, making production waste management both efficient and cost-effective. - Flexible, Scalable Solutions
Outsourced recycling offers flexibility to adjust volume requirements as production needs change. A partnership with C-Square Polymer provides scalability, allowing manufacturers to handle variable production levels without the need to modify internal operations. This is especially advantageous for businesses with seasonal production cycles or unpredictable demand. - Focus on Core Operations
By outsourcing recycling, manufacturers can concentrate on core competencies, like product innovation and client service, rather than managing recycling processes. Additionally, partnering with a reliable recycler often simplifies compliance, as experienced providers maintain necessary documentation and follow environmental regulations.
- Dependence on Third Parties
Relying on an external partner introduces potential risks, as manufacturers become reliant on their recycler’s capacity, timeliness, and quality control. Unexpected disruptions in outsourced services may temporarily impact production, especially if alternative recycling options aren’t readily available. - Customization Constraints
Outsourced recycling may offer less flexibility when it comes to tailoring processes for unique material specifications. For companies requiring highly specialized recycling processes, in-house operations may offer a higher level of customization. However, a partner with experience in post-industrial materials, such as C-Square Polymer, often offers solutions tailored to meet a variety of industry demands. - Coordination and Compliance Tracking
Outsourcing requires close communication with the recycling partner to track data and meet regulatory requirements. Coordinating with a third party for compliance documentation can add an administrative layer, making clear communication essential.
Here’s a table summarizing the pros and cons of in-house vs. outsourced recycling for plastic manufacturers:
Aspect | In-House Recycling | Outsourced Recycling |
---|---|---|
Control Over Quality | Complete control over quality standards and material consistency, ideal for high-spec materials | Quality control in partnership with expert recyclers; potential access to industry-leading processes. |
Efficient Material Flow | Faster turnaround and seamless flow of recycled materials, reducing dependence on external suppliers. | Flexible access to recycled materials without maintaining inventory; less supply chain disruption. |
Environmental Branding | Directly managed recycling enhances green brand image and ensures compliance with sustainability goals. | Enhances sustainability profile with minimal internal adjustments; experienced partners handle compliance. |
Cost Efficiency | Avoids ongoing service fees and potential long-term cost savings after initial investments. | No upfront capital investment; lower operational costs by relying on a specialized partner. |
Flexibility and Scalability | Limited by facility size and capacity; may be costly to scale. | Scalable without infrastructure changes, ideal for fluctuating production volumes. |
Focus on Core Operations | May detract resources and focus from core production activities. | Allows manufacturers to focus on core competencies, like innovation and customer service. |
Capital Costs | Requires significant investment in equipment, space, and skilled labor. | Outsourced options are generally more cost-effective, avoiding capital expenses. |
Resource Allocation | Diverts resources toward recycling operations, adding complexity to production. | Minimal impact on internal resources, though coordination with external partners may be required. |
Scalability Constraints | Scaling is limited by available facility space and equipment capacity. | Easier to scale up or down in response to production demands. |
Dependence on Third Parties | Not dependent on external providers; reduces risk of supply chain issues. | Relies on recycler’s capacity and quality standards; service interruptions may impact production. |
Customization Limitations | Full control over customization for specific material requirements. | Limited customization; dependent on recycler’s material processing standards. |
Compliance Coordination | Direct oversight on compliance but requires in-house resources for reporting and monitoring. | Compliance is handled by experienced recyclers, although regular coordination is necessary for tracking. |
Why C-Square Polymer?
For plastic manufacturers considering outsourcing, C-Square Polymer provides a reliable, scalable solution with specialized expertise in recycling a range of post-industrial materials. Handling over 3500 tons of plastic waste annually, we transform scrap materials from production into high-quality recycled compounds suitable for new applications, reducing reliance on virgin resources. By recycling a diverse mix of plastics, we help manufacturers lower environmental impact and achieve sustainability goals, with greenhouse gas emission reductions equivalent over 7,900 tons of CO₂e each year.
Our expertise in managing complex, post-industrial waste makes us a preferred partner for manufacturers aiming to streamline recycling while improving sustainability outcomes. With C-Square Polymer, companies can feel confident that their recycling needs are in expert hands, enabling them to concentrate on production and innovation.
Conclusion
Deciding between in-house and outsourced recycling comes down to evaluating costs, scalability, and sustainability goals. In-house recycling provides quality control and production efficiency but requires significant investments and resources. Outsourcing offers flexibility and expertise, allowing manufacturers to stay focused on core operations while meeting environmental standards.
For those looking to leverage a specialized, reliable recycling partner, C-Square Polymer delivers industry-leading recycling for a wide array of post-industrial materials. Partnering with C-Square Polymer means transforming waste into a sustainable resource, empowering businesses to optimize production and reduce environmental impact.
Featured image by macrovector on Freepik | Inline image by frimufilms on Freepik